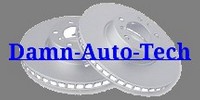
For a safe secure mounted vehicle see Jtis's jacking/lifting procedures! Safety should always be your first choice!
FAILURE TO FOLLOW SAFETY INSTRUCTIONS MAY RESULT IN PERSONAL INJURY.
Changing worn-out (discard thickness) brake-discs
Use Jtis information, of how to dismantle the front/rear brake system. Place a cloth over and under
the master brake cylinder, pressing back caliper pistons could over flood the brake-fluid reservoir with resulting
spillage (brake fluid is an aggressive, poisonous, hydrogenous substance, avoid paint contact, neutralize (immediately!) through
lots of water. Poisonous, if consumed, a few millilitres are life threatening, always keep it in its original packaging, do not
fill it in bottles (recognition problem). Hydrogenous, brake fluid likes to saturate itself with water,
keep brake fluid containment air tight, a day of saturation would make it unusable, the absorbed moisture would have reduced its
boiling point by a (few) hundred degrees. As we know fluids are not compressible, gases are. A Braking system can
get very hot, dissipating heat directly to the caliper pistons and therefore to the brake fluid itself. Is the fluid water saturated, then it
starts to boil earlier, (gas bubbles build) leading to brake fading or no braking at all. Not to mention
high altitude, mount ranges, braking down hill. Change brake fluid regularly! its also a protection against corrosion
of your car's braking system (ceasing of ABS hydraulic unit, ceasing of caliper pistons, early worn master/slave brake and clutch cylinders.
Check brake hose for damages like cracks, bites, ware, hardness, squeeze and bend if it is still flexible everywhere.
Don't let the caliper hang on its brake hose, bind it up.
Brake fluid - ITT Super Dot 4
Caliper slide pin grease - Klueber GLK1
Front Brake-Disc:
Brake disc diameter - 300mm
New disc nominal thickness - 30mm
Worn disc discard thickness - 28mm
Max. disc run-out (installed) - 0.076mm
Max. thickness variation new disc - 0.005mm in 360°
Max. thickness variation used disc - 0.009mm in 360°
Wheel nuts - 128Nm
Caliper anchor bracket - 103Nm
Caliper retaining bolt - 34Nm
Rear brake-Disc:
Brake disc diameter - 288mm
New disc nominal thickness - 20mm
Worn disc discard thickness - 18.5mm
Max. disc run-out (installed) - 0.05mm
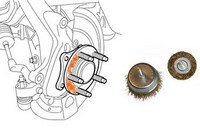
Clean, remove only rust from the hub face, wheel retaining bolts, through the use of a circular or steel brush and anti rust spray. Don't use files, sand paper or any-other metal removing technique (no adhesives). After cleaning, apply anti-rust spray a corrosion inhibitor, let it work, wipe the un-dried rest off. Why rust inhibitor, rust builds enormous expansion pressure that would, after time bring your brake-disc to wobble and out of its specification, don't use grease or oil here, this would definitely change the heat dissipation between hub face and brake-disc.
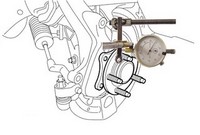
Check the hub's face run-out, that, it runs in its specification. A hundredth millimeter of wobble here is about 0.02mm-0.03mm at the outer edge.
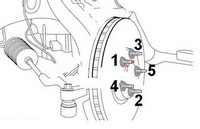
Read the brake-disc manufacturer’s instruction, if a removal of the anti corrosion coating is necessary, if so, clean thoroughly (Acetone). On the cleaned, corrosion protected, rust free, running in its parameters hub face, set the brake-disc, wheel nuts, torque to 20Nm evenly (see numeric pattern).
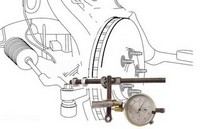
Hookup a dial-gauge, set gauge 10mm from outer edge (set to 5), rotate brake-disc slowly, observe dial needle (high/low), note measurement, if out of range, un-mount, turn disc one hole further (see self-made mark), repeat procedure again until minimal run-out has been achieved.
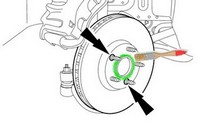
Restore disc retaining clips, apply a slight coat of grease around the hub disc/wheel center, this will prohibit wheel-rim from corroding to the hub. Don't oil/grease wheel nuts/bolts, by doing so, you will increase the applied wheel nut/bolt torque up to 30% and therefore put more stress on the nut/bolt, thread, causing excessive wear and lowering its lifespan, just use a steel-brush to brush them off and apply a bit of graphite powder. Clean wheel-rim, its mount-area, check tire for damages, torque to specification, always use a torque wrench, this will apply an even pressure on the brake-disc, therefore preventing the break disc from warping at high braking temperatures. See the above, torque wheel in numerical order.
General Service Information
General Service InformationRear axle
Rear sub-frameFront axle
Lower ball-point joint, Shock absorber bushes, Stabilizer bar links + mountsBrake disc and pads
Engine
Intake Manifold / Ignition Coils / Spark-plugs/ engine-block ventilation (elbow)Injectors
Starter system
Valve clearance, timing-chain, tensioner and glides:
With valve clearance in its tolerance,
there was no need to take the camshafts down, so tensioners and co. have to wait, the good thing is the
tensioner pumps up in 3-4 min. the rattle noise disappears.
Cruise control malfunction, emergency mode
Automatic Transmission 5R55N
Info, tips, Fail Safe ModeStall Speed Test procedure and diagnoses
Valve Body, known issues
Valve Body, Solenoid test procedures
Line Pressure Test
Self made press for pressing down clutch drum springs, checking clutch tolerance without a dial gauge
Chassis
Air ConditioningMiscellaneous repairs
Wind-shield-wiper mechanism:
Time on the lot took its toll, wind-shield-wiper shafts had seized,
uninstalled the mechanism, freed the seized shafts through the use of a good rust loosener, heat, force.
Water in Spark-plug wells 3-2 cylinder:
After days of heavy rain the engine began to misfire with
accounted trouble codes, spark-plug wells were wet, an ionized rusty red path on the ceramic insulator had developed which shorted the
HV ignition spark.
Radio:
Connected the radio controls to the multi-functional steering wheel using
an analog digital converter.